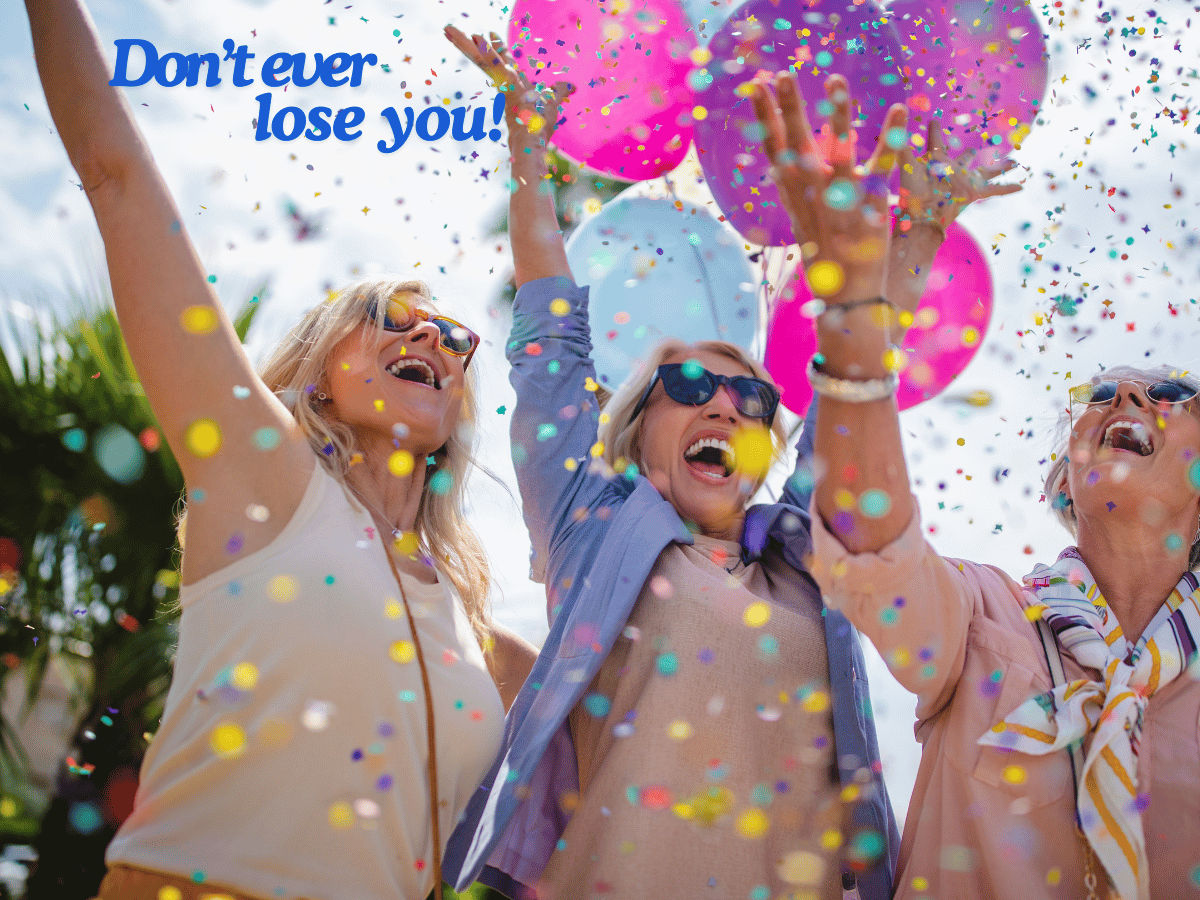
Materials out of stock mid-project is a common challenge faced by many project managers. This situation can disrupt project timelines, lead to cost overruns, and even compromise the overall quality of the end product. Understanding how to effectively adapt your project plan when facing a materials shortage is crucial for maintaining project momentum. This guide provides a comprehensive approach to managing materials out of stock scenarios mid-project, offering practical solutions and strategies for mitigating potential risks. We’ll delve into proactive planning, alternative materials sourcing, and timely communication strategies, and even discuss strategies for reducing project delays. Learn how to overcome these disruptions and deliver successful projects. This article will explore various strategies, from communication and procurement to contingency planning.
Understanding the Impact of Materials Shortages
Identifying the Root Causes
Material shortages are often caused by unpredictable events in the global supply chain. Unexpected disruptions can significantly hinder a project’s progress. Delays in delivery times can lead to significant impacts. Understanding these potential disruption points can help project managers be proactive and prepared for similar issues in the future.
Evaluating Project Impacts
Material shortages often result in delays and cost overruns. These impacts can cascade throughout the project, affecting not only the budget but also critical timelines. The inability to acquire necessary materials can lead to project schedule slippage. If projects aren’t ready for these challenges, they can fall behind schedule. Teams might even encounter a need to re-evaluate budget allocation, potentially leading to cost overruns. Failure to plan ahead for these potential challenges can be quite detrimental to a project’s success.
Proactive Strategies for Mitigation
Proactive steps can drastically reduce the impact of a material shortage. One key strategy is to maintain a robust supply chain management system. Establish clear communication channels with suppliers to anticipate potential issues and proactively address them. Building in buffer time into project timelines can also help to mitigate potential delays. This contingency plan should include exploring alternate vendors, substitute materials, or adjusted project scope if necessary. Early identification and response are crucial to minimizing the impact on project timelines.
Related Post : Unexpected Issues Behind Walls? Handling Surprises Without Panic
Exploring Alternative Materials and Vendors
Identifying Substitute Materials
Investigating and evaluating suitable substitute materials is essential for minimizing project delays. Identifying and considering alternatives requires research and careful comparison. This includes factors like technical specifications, cost, and availability. Analyzing these components can help identify a viable alternative, leading to project continuity. This requires a robust vetting process to identify potential substitutes.
Expanding Vendor Options
Expanding the range of suppliers can provide a safety net in case of delays from a primary supplier. This process should involve a thorough review of supplier capabilities and track records. Building relationships with multiple reliable suppliers is an important aspect of managing potential supply chain risks and is crucial for minimizing disruptions. Having alternative vendors ensures continuity and helps maintain project timelines.
Evaluating Material Cost Implications
Carefully evaluate the cost implications of substitute materials. Consider not only the upfront price but also potential long-term costs. Factors like material durability, labor costs for installation, and potential quality issues should also be analyzed. Consider the possibility of future increases in costs if you only use one vendor or supplier. These factors can have a profound impact on the overall project budget.
Adjusting Project Scope and Timeline
Evaluating Project Scope
In cases of critical material shortages, a necessary but sometimes difficult step is reassessing the project scope. Identifying non-essential components can help reduce the overall material requirements. This strategic approach allows for adjustments to accommodate available resources and material availability.
Implementing Flexible Timelines
Employing flexible project timelines allows for adjustments based on the availability of materials. Implementing a buffer period for potential delays can help mitigate the negative impact of a materials shortage. This can involve re-evaluating deadlines and tasks to find a suitable compromise for both stakeholders and project timelines. This approach needs to consider how stakeholders will view the timeline changes.
Communicating Changes Effectively
Clear and concise communication with all stakeholders about scope and timeline adjustments is crucial. Clearly outline the rationale for the changes and address any concerns promptly. Open communication fosters trust and understanding, enabling successful project completion despite challenges.
Implementing Contingency Plans
Establishing Contingency Funds
Establishing contingency funds for unforeseen material shortages is crucial. This financial buffer will help absorb the cost implications of procuring substitute materials or adjusting project timelines. It ensures the project is prepared for any potential financial impact of delays or alternative costs.
Creating Detailed Risk Assessments
Detailed risk assessments help anticipate potential material shortages. Identify potential risks and develop mitigation strategies, including backup plans for alternative materials and vendors. These strategies will help manage project delays effectively, helping to maintain a suitable project timeline.
Implementing Project Monitoring
Continuous project monitoring is critical for timely identification of material shortages. Regular communication with suppliers, close tracking of material delivery schedules, and proactive communication with all stakeholders can effectively mitigate disruptions to the project’s progress.
Maintaining Open Communication
Regular Stakeholder Updates
Keep stakeholders informed throughout the process. Regular updates provide transparency and address concerns promptly. Transparency in communication builds trust and keeps all parties informed of the situation.
Addressing Stakeholder Concerns
Actively address concerns and proactively anticipate issues related to materials shortages. This transparency prevents misunderstandings and fosters a collaborative environment. This collaborative approach promotes effective problem-solving and reduces project delays.
Documenting Communication History
Maintain a comprehensive record of all communication regarding materials shortages. This documentation will prove valuable in case of disputes or future projects, and it will improve communication efficiency in the future.
In conclusion, navigating materials out of stock mid-project requires proactive planning, adaptable strategies, and a willingness to explore alternative solutions. By prioritizing communication, exploring vendor options, and considering flexible project timelines, teams can successfully overcome these challenges and deliver projects on time and within budget. Remember, preparedness and adaptability are key to mitigating the impact of unforeseen circumstances. Contact us today to discuss how we can help you avoid disruptions in your future projects. Let us help you find solutions for Materials Out Of Stock issues!